Interview With Infill Plane Maker Bill Carter
After spending most of his working life as a carpenter and cabinetmaker, forty-eight year old Bill Carter decided that he would like to make handplanes for a living from his home workshop in Leicester, England. That was in 1987 and although he had made many wooden planes before this time, almost all of his planes since have been dovetailed in metal or cast – and all of them are completely hand made. Since turning to planemaking full time, Bill Carter has made and sold some 700 planes – an impressive number for a one man operation!
Most of Bill’s planes are box type or original pattern mitre planes, although he has made other styles including 28-1/2 inch jointers. Bill uses mostly reclaimed materials for his planes including brass tenon saw backs, old boxwood chisel handles, rescued Cuban Mahogany door rails and any other suitable material that comes his way. He also uses older cutting irons for almost all of his planes and often antiques the finished planes with various chemical concoctions to make them look more authentic.
In 1992 Bill Carter was featured in the February edition of the British magazine “Woodworking Today” (issue number 28). It was in this magazine that the interviewer C.R. Miller – himself a fledgling maker of dovetailed planes at the time – first learned of Bill. In 1999 Bill Carter chatted by phone for the first time to Handplane Central.
H.C. – Can you give us a brief history of your background prior to planemaking? Did you have any specific skills such as engineering that may have helped you in the making of handplanes?
Bill Carter – I’ve had no engineering at all but I was a joiner by trade and I’ve always been good at woodwork. One day I read about how to make a Norris plane in a magazine. You could send away for plans so I did that. The fellow who made the plane had done it in college and he lived not far from where I live in Leicester. The plans were for a panel plane but I made my first plane much longer using the same techniques. I made it into a 28 1/2″ jointer.
H.C. – Did you use Rosewood for the infill or did you use another timber?
Bill Carter – Yes I did. I’ve made four jointers and I’ve used Rosewood in all of them.
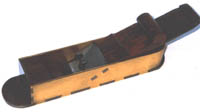
H.C. – So what year did you start making planes?
Bill Carter – Well I don’t know what year I started making wooden planes because I’ve made them for some time,and I can’t remember exactly when I started. I also used to make quite a few gauges early on as well, with nice timbers and also brass faced. I left the museum, which was my last job, in 1987 and directly after leaving the museum I started making trying to make a living making planes.
H.C. – Were these wooden or metal planes?
Bill Carter – No, it must have been around about then when I made my first metal plane. On one of my planes that I’ve sold somewhere in America I did put a load of jargon stamped into it including “Established 1987”. I’ve written quite a lot of little bits on planes in the past, saying things like “Planemaker to the gentry”, which I frequently use as well as other things.
H.C. – Where do you write that? Do you write it on the bed or somewhere else?
Bill Carter – I stamp it on the front of the plane, on the toe. I originally made quite a lot of small mitre planes out of tenon saws and I don’t think anybody had ever done that before I did it, and so I’ve written about that on one or two planes.
H.C. – So did you have stamps made up or did you use ordinary letter stamps?
Bill Carter – When I do a long sentence I use individual letters, but I’ve had various marks made in Sheffield with my name on them. I’ve got about six or seven marks.
H.C. – Why so many different marks?
Bill Carter – Because I’ve gone on from one thing to another. The first mark I had which I put on my planes was “Carter” with a zig zag border. I was copying the old makers from the late 18th Century but that mark didn’t stamp very easily on some of the metals, so I had a script mark made which stamps into the metal much easier. I’ve gone on to have various marks since then. I very often use “London” instead of “Leicester”. Sometimes I’ll put “Carter Leicester”, sometimes “Carter London” and every now and then “Carter Leicester & London” or just “Carter”.
H.C. – Well that will get the collectors thinking in 100 years time, won’t it?
Bill Carter – Well it already has, but some of the early planemakers over here used to put “London” even if they came from Birmingham or elsewhere, so I just thought if it was good enough for them, it’s good enough for me. A lot of people who know I make planes in Leicester still ask me frequently why do I put London on them, so I always tell them. It’s also a more convenient size. Leicester is such a long word and if I put ‘”Carter London” it’s the same amount of letters and it looks neater.
H.C. – What sort of difficulties, if any, did you encounter when you first started making planes?
Bill Carter – I had no problems with the dovetails, but I did have problems with the riveting because I did everything by hand, and drilling through a three inch plane is a bit tricky. I still do everything by hand. I couldn’t make lever caps and screws and I couldn’t do adjusters either, but most of my planes even now don’t have them, and I always buy them in when they’re needed. I make the pattern, for say the lever caps, and have them cast and then I’ll quite often file them.
I haven’t got any machinery whatsoever to do the screws or adjusters so I farm them out. That was the difficulty… it was a great difficulty trying to get those made and it took me quite a few years before I found someone, just recently, who’s prepared to do it and that turned out to be a local engineer. Also, when I started to make mitre planes I couldn’t find any engineers who would machine the angles necessary for the mouth on the sole or the tongue and groove joint, so I had to do that all by hand as well – which isn’t easy either.
H.C. – Approximately how many planes have you made to date?
Bill Carter – About seven hundred. My wife says I’ve made more but it’s around about 700. Most of them have been sold and I’ve given some away. I’ve only got about five or six of them in stock.
H.C. – Do you make planes first, which are then subsequently sold, or do you make them to order? Do you do a bit of both?
Bill Carter – I nearly always make them and then sell them. I’ve only been commissioned half a dozen times because I tend to make rare early English planes that I like making. People have approached me and asked me to make a wooden plough plane but it’s so complicated to do and it’s not worth much at the end of the day so I’ve always refused to do it. I just want to do what I want to do – which is to copy rare planes – and please myself. I never know from one day to the next what I’m going to be making.
H.C. – Are most of your planes sold to British buyers or do many of them go to Europe or America?
Bill Carter – I don’t really sell them direct very often, but they have gone all over the world. I know they’ve gone to Canada, North and South America, Australia, Germany, Ireland, France and other countries. I originally used to put the planes in auctions and I also never used to put my name on the first ones I’d made.
Some of them would sell for more than the originals because people assumed they were genuinely old. I always colour and age my planes, and I nearly always use old materials whenever possible.
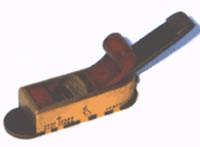
H.C. – Why do you have a preference for using old materials rather than new?
Bill Carter – Well, because the older materials usually have a better colour, especially brass, and I’m always trying to copy a period and the older materials just fit in.
H.C. – So you’re trying to recreate the period in which they were originally made as well as the styles they used?
Bill Carter – That’s right, yeah, but I also use gauge plate for a lot of my planes – which is a new material – but only because I can’t get any better suited steel. Karl Holtey, I’m led to believe, uses mild steel as do some other makers I know about, but I use gauge plate because it’s machined to close tolerances and I don’t have to mess about with it. If it says that it’s 1/8″ thick and 2″ wide then I can trust it.
I’ve only ever made one or two planes from mild steel. With gauge plate I also find that it’s easier to knock the waste material out from a dovetail than it is with mild steel. When I’m making dovetails I cut several slots in the waste material so that it looks a bit like a comb, and then I knock them out with a chisel. They break exceptionally easy with gauge plate, but not so easily with mild steel.
H.C. – That would have to do with the makeup of the two steels. Gauge plate is a tool steel with a higher carbon content than mild steel, and it does fracture more easily as you said. It’s also tougher and harder wearing than mild steel, so it’s an excellent choice for sole plates, for obvious reasons. Having said that though, I’ve not used it myself for sole plates, but I do know people who have.
Bill Carter – I’ve also tried to get wrought iron – genuine wrought iron – but it’s unobtainable over here, although I have had a little bit of second hand stuff.
H.C. – I’ve never used wrought iron myself, despite the fact that there are four separate blacksmithing businesses in the same factory complex as C. R. Miller Planes. One or two of those blacksmiths have access to limited stocks of old wrought iron but I’ve yet to persuade them to give me some. I think it would be pretty interesting to use a bit of wrought iron though.
Bill Carter – Yes, it is. It’s very, very different to work. I’ve had various pieces of it – all from the one source and all of them were rusty – but because it’s built up in layers and laminated, as soon as you start hammering away and peining it, it can separate – which can be a bit strange. I recently made a skew mouthed mitre plane with wrought iron and it was the first time I used it on the sole. That was when I found out that it can separate. I made the bridge out of it as well – with double tenons – and of course when I spread the tenons on the outside of the plane it did separate into about four pieces.
H.C. – That would make you a bit panicky, especially if any of the pieces had broken off?
Bill Carter – Yes, it would have except I was fortunate enough that the steel was very, very malleable and it did spread quite easily.
H.C. – So was that plane an improved pattern mitre plane or the box type?
Bill Carter – It was the original box style. I’ve got various drawings of early planes that I’ve had in my collection from time to time. I’ve had a small Holtzapffel mitre plane and quite a few by Buck, and I’ve taken drawings of them. Most of them were about four or five inches long – roughly half size, I suppose.That particular plane was based on a Buck pattern, but with a skewed mouth. Original mitre planes with skewed mouths are exceptionally rare, but having said that somebody has told me that they actually have a skew mouthed Holtzapffel miniature mitre plane but I haven’t seen it. I think that one would be extremely rare indeed.
H.C. – Do you get a lot of your patterns from existing planes?
Bill Carter – Yes, I do. In actual fact I don’t make too many different types of planes. I’ve made jointers but the majority of my planes have been mitre planes – from full size right down to miniature. That’s really the bulk of all the planes I’ve made. I’ve made lots of variations of wooden planes but I don’t really count them. I’ve started to make copies of the Mathieson thumb plane because again it’s an extremely rare pattern over here in England. I had an original Mathieson thumb plane myself and I dearly loved the shape of it. As far as I know there’s only been two original Mathiesons found and I had one of them. I like chariot planes and I have made a few of them, but it’s mainly mitre planes that I make.
H.C. – Do you prefer making the older box style mitre plane to the improved pattern or is there just more of a demand?
Bill Carter – I don’t really prefer them but I’ve only made the odd one or two improved patterns. The older version is quicker and easier to make, and of course they were the first metal planes made in Britain. I guess everything else was developed from them. I recently sold one of the prettiest gunmetal mitre planes I’ve ever seen in my life. I think it was English but I don’t know for sure. It had one of the most beautiful wavy top along the sides, and one day when I’ve got the time I’ll make a few copies of it.
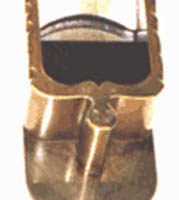
H.C. – I’ve seen a photograph of one of your mitre planes in gunmetal which looks like a very thick casting, yet it has a dovetailed sole. Can you tell me how you went about making this plane?
Bill Carter – When I was making my jointer right back at the beginning, the process took so long that part way into it I thought I’d get a casting made up of a mitre plane while I was getting the lever cap cast. So even though I started making the jointer, that mitre plane was actually the first ever metal plane I finished. I had an original one in my collection which I took the pattern from and it was basically a hollow gunmetal casting which I dovetailed a steel sole on.
H.C. – Do you still have that plane or did you sell it?
Bill Carter – I did sell it to a friend of mine for around £600, I think.
H.C. – Speaking of prices, what sort of range do you charge typically for your planes?
Bill Carter – Well I’ll charge any price which comes into my head. I never have fixed prices. I’ve been paid as much as £3300 for a jointer but at the same time I’ve sold one of my jointers for £1000, because at the time I was a bit short of money.
H.C. – Were they both the same size or was one longer than the other?
Bill Carter – The four jointers I’ve made have all been exactly the same size, although I’ve done various decorations on them. I put a lot of cupids bows on the jointers – on the front, the back and the escapement. I do rather like the cupids bow design and I incorporate it on most of the planes I make.
H.C. – I tend to use it mostly on the smaller planes like chariots, thumbs and small mitres, but I have used them as well on some smoothers. I usually always have them facing downwards as well, although older planes seem to have them in either direction – facing up towards the user or down towards the mouth.
Bill Carter – Yeah, I love cupids bows, and of course they’re typical of early English planes and that’s another reason why I like to use them.
H.C. – You mentioned in an article many years back that you wanted to make a 36 inch jointer. Have you done anything about making that at all?
Bill Carter – Last year I got some steel in the right length to do a 36″ jointer but I’ve got to get some bronze for it. I bought some bronze about seven years ago and I remember that I didn’t really like the colour of it at the time. Recently though, a friend of mine offered me one of my planes back that I’d made for him the bronze. When I went over to look at it I saw that the colouring and the patina on it was fantastic, and because I got all excited about it he wouldn’t sell it back to me. What I did was come home and make another one, which I’ve just finished.
Now I intend to get some more bronze and I’ll use that for the sides of the jointer. It’s also a matter of getting around to it but I’ve been meaning to make a 36″ jointer for a long time now – almost as long as I’ve been making planes.
H.C. – I’ve got one that’s almost half way made and that’s in steel, but like you I’ve just got to get around to finishing it.
Bill Carter – Well, originally the very first jointer that I’d made was supposed to be 36″, but at the time I couldn’t get 36″ material so it ended up being 28 1/2″.
H.C. – Can you get gunmetal over there in England? Is it readily available in sheets or strips?
Bill Carter – No, not really. There are foundries – and in particular one famous one here in Leicester called Harrisons – who can cast gunmetal for lever caps and the like, but they won’t do 1/8″ sheet. I don’t think it’s economically viable for them. You can get 1/4″ though, and even thicker, but they won’t do 1/8″ thick.
H.C. – I haven’t found anyone in Australia who can supply me with 1/8″ thick gunmetal sheets or strips unless I order twenty thousand tonnes, which is a bit out of my league. Foundries will cast gunmetal patterns without any difficulty, however, but the sheet gunmetal has pretty much been superseded by the newer bronzes such as phosphor bronze, manganese bronze and silicon bronze.
Bill Carter – I think it’s much the same here.
H.C. – Have you been featured in many publications at all?
Bill Carter – I’ve just done an interview with “Furniture and Cabinetmaker” a few weeks back and that will probably appear in article form later on in the year. A friend of mine has written the story of my planemaking and he sent it over to America, but nothing’s come of that yet. He also got in contact with Garrett Hack who wrote “The Handplane Book”, and who is now writing another book, which apparently I’ll be mentioned in. He didn’t know of me when he did the first book.
Garrett Hack and his photographer came over to England in March of 1998, and they spent a day in my workshop photographing bits and pieces.
Incidentally, I gave him a plane and apparently when he travels around America giving talks and demonstrations, he takes my little mitre plane and shows people and I guess talks about it. He maybe even uses it because he’s a woodworker by trade as well as a writer.
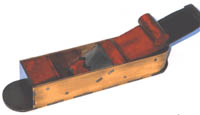
H.C. – Do you use any of the planes yourself, in general work?
Bill Carter – Yes, I do. I always use my own planes in planemaking. I also use a Norris and a Stanley, but when I’m doing a bed or something intricate like the front infill on a small mitre plane I use my own planes because they’re suited for the job.
H.C. – Do you use floats or anything else for the beds?
Bill Carter – I’ve got floats but I never use them. I mainly use a modified chisel.
H.C. – Can you give me a quick rundown on the sort of hand tools, power tools or machinery you use and also a description of your workshop?
Bill Carter – My workshop is just a garage which I built in 1962 from asbestos sheeting and timber. It’s extremely cold in the winter so I don’t work then. The only power tool I use regularly is an 8″ grindstone for the irons. Out of seven hundred planes about six hundred and ninety have been reclaimed old Sheffield – made irons, so I regrind them and cut them to the right width. I occasionally use a power drill but otherwise all I use is hand tools – files, chisels, handplanes and the like.
H.C. – Do you use any special jigs or templates?
Bill Carter – No, nothing really, except for wooden bending formers for the round backs of the mitre planes. They’re just rounded over bits of wood that are held in the vise. One day I’d like to get some metal formers made because that would make it a lot easier. I always cold work the metal but once it’s bent I sometimes anneal it to stop it from snapping when I open it up again to put the bridge in – especially on the smaller planes.
H.C. – Yes, annealing does make things a lot easier. Where do you get your design ideas from? Do you experiment much with your planemaking in regards to different bedding angles etc?
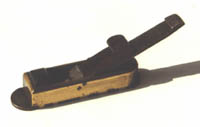
Bill Carter – I have with mitre planes. A lot of the mitre planes I make are so small that I can’t get a really low bed angle so I have to do them higher. I’ve made mitre planes from twenty – eight degrees right down to twelve and a half degrees. I don’t really notice much difference between them. They still work just as well, both on end grain and side grain. It’s probably because I do pay very special attention to fine mouths and good cutters.
H.C. – Have you done any exhibitions or shows demonstrating planemaking?
Bill Carter – No, I’ve never advertised and I don’t go anywhere other than the tool sales, but last year I was asked to do an exhibition in Munich, Germany, which was a big honor. I had to turn it down and in fact I put them on to Karl Holtey and he actually went and exhibited his tools at this trade fair. I turned it down because I would have had to have been there for a week and I don’t really like talking in person to a lot of strangers. I don’t mind talking to people one on one about planemaking, but I don’t really like talking to groups. I also can’t speak German, which would have made it a bit difficult.
H.C. – You mentioned Karl Holtey before, do you have much involvement or interaction with other planemakers?
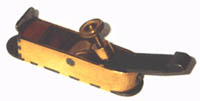
Bill Carter – I’ve never, ever watched anybody else actually making a plane, but I do know three or four people who have made them at some stage, including Karl Holtey. Karl, in particular, keeps inviting me to come to his place but I haven’t been yet. I’ve seen the results made by Karl and various others, but I’ve never actually seen how they’ve been made. Karl has said that he wants to see me do the mouth escapement because he’s amazed that I do it all by hand and he just can’t believe it. I see Karl quite a bit, and when I need adjusters I buy them from him because they’re so fantastically made.
H.C. – Does Roy Shuter still make any of your adjusters or do you only use Karl Holtey’s now?
Bill Carter – Well, Roy would do them for me if I asked him to, but Karl Holtey’s are better. They’re much more precise, and if I ever need an adjuster I go to Karl because I’m always trying to get the very best that’s available and his adjusters are just so superb. You’ve only got to handle one of them to see that he’s a perfectionist. The engineering is second to none. I really don’t think anybody could make a better adjuster than Karl Holtey – they’re just so wonderful.
H.C. – Yes, I’ve heard much about them but I’ve yet to check them out. How long would it take you to make a mitre plane on average – without an adjuster?
Bill Carter – It usually takes about two weeks, but the first jointer I made took about three months because I wasn’t accustomed to it. I eventually got them down to three and a half to four weeks.
H.C. – Have you made coffin smoothers at all?
Bill Carter – No, I’ve done drawings of them because again, I’ve always wanted to incorporate a cupids bow – and to make a smoother in the same pattern as my jointers it works out to be quite large. Also, smoothers are common over here whereas mitre planes aren’t, and I can get a higher price for my mitres than if I were to make smoothers. All of the planes I’ve made are one-offs. I’ve never made two alike, and all the mitre planes and jointers are absolutely individual.
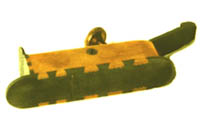
H.C. – So I take it you don’t use a standard set or spacing for dovetails and the like?
Bill Carter – No, I’ve done every shape of dovetail under the sun. Different spacings between them, different angles, dovetails variegated from front to back, I’ve done all of that. I’ve even done a small mitre plane with cupids bow dovetails and again, I know of no – one else who’s done that.
H.C. – So the side of the plane is relieved into the sole with a bow shape is that right? Or is it vise – versa?
Bill Carter – Yes, that’s right. The steel sole is relieved in the cupids bow shape, and the brass side is worked into it. It’s a bit scary because you don’t know if you’ve done it right until you clean it up, so it has the potential to be very much hit or miss.
H.C. – It sounds pretty impressive. I might try that out myself if that’s O.K. with you?
Bill Carter – Yeah, sure. That’s fine with me. I’ll send you a photograph of that plane, along with some others.
H.C. – That would be great. Well that’s pretty much it for the questions. Thank you very much Bill, for talking with Handplane Central Online about your planemaking.
Bill Carter – Thank you for letting me be a part of it all.
Bill Carter can be contacted at:
98 Havencrest Drive
Leicester LE5 2AH
United Kingdom
Check out some of Bill Carter’s tips and tricks for making wooden and infill planes.